Theoretical part
Construction of the robot "Robot Arm":
The general appearance of the 6DoIt Mobile Robot Arm (6DMRA) is shown in Fig. 5. Its kinematic scheme is shown in Fig. 6.
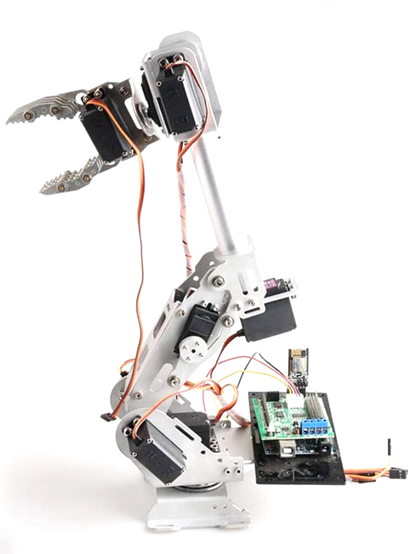
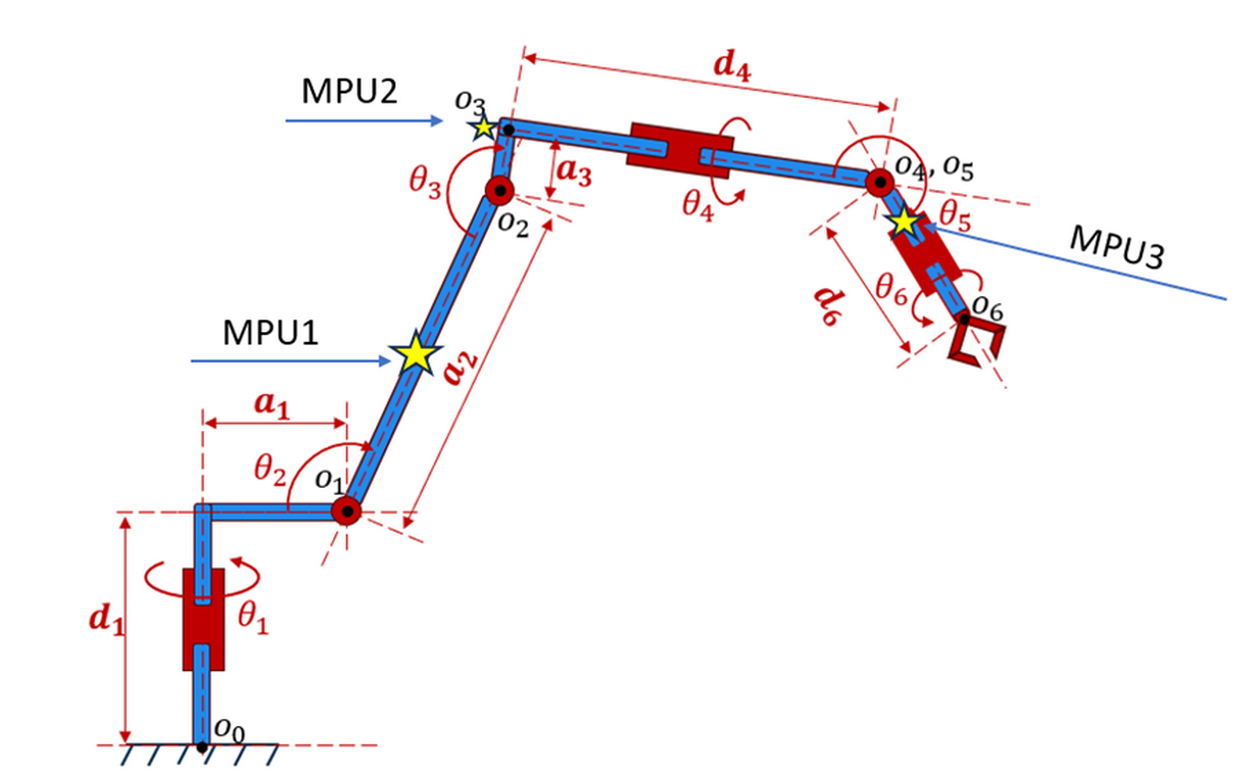
The 6DOF DoIt Mobile Robot Arm is a smaller version of industrial work with 6 degrees of freedom. This small manipulator weighing up to 1 kg with a maximum load of up to 0.5 kg can be mounted on a solid surface, installed on a table or on a special cabinet. The work base can be turned up to 180°.
The robot consists of six kinematic pairs. Each kinematic pair has its own geometric dimensions determined by parameters
Axis | Connection angle (θі) | Link twisting (αі) | Link length (aі) (mm) | Link shift (dі) (mm) |
---|---|---|---|---|
1 | θ1 | -90° | 45 | 75 |
2 | θ2 | 0° | 115 | 0 |
3 | θ1 | -90° | 20 | 0 |
4 | θ4 | 90° | 0 | 130 |
5 | θ5 | -90° | 0 | 0 |
6 | θ6 | 0° | 0 | 50 |
The working zone of the manipulator robot in the reference plane is determined by the inner and outer radius of the working surface. The inner radius of the working surface is 65 mm, the outer radius is 340 mm.
DENAVIT-HARTENBERG METHOD
Each kinematic joint (kinematic pair) of a 6DOF robot is rotational and has one degree of freedom of movement. The movement of the movable link of the articulation is determined by the so-called generalized coordinate - the angle of rotation
When the manipulator moves in the working area of the robot, the generalized coordinates of each joint change, forming the grip movement trajectory. Having six manipulator joints, the 6DOF robot can adopt different geometric configurations of links at a given gripper positioning point. Therefore, it is important to be able to determine the absolute coordinates of the position of the links to control the geometric configuration of the manipulator in accordance with the given one.
The grip positioning point
In the case when the absolute coordinates of the links are known, the grip position is determined uniquely in the
- Binding of coordinate systems to links of the manipulator.
- Determination of parameters of links and joints.
- Construction of homogeneous transformation matrices.
Binding of coordinate systems to manipulator joints. To bind coordinate systems to each joint, the following rules must be followed:
- Set the manipulator to zero (initial position).
- The
axis must coincide with the axis of rotation or the axis of translational motion st link. - The
axis must be perpendicular to the st link and cross this axis. The axis is freely chosen. - The
axis is the vector of multiplication and creates a right coordinate system.
Taking these rules into account for the DMRA robot, we have the following orientation of the joint coordinate systems (Fig. 7).
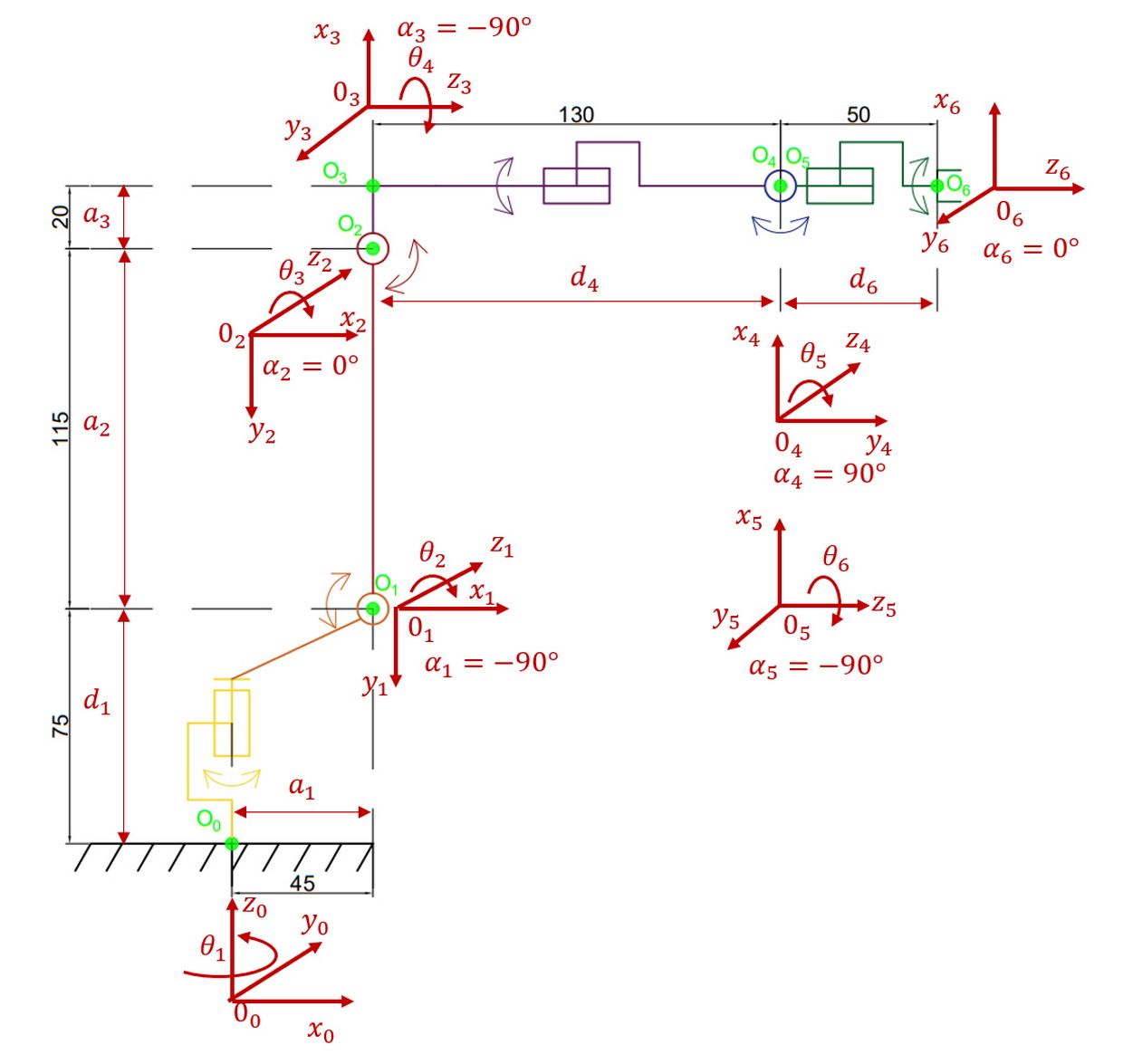
Determination of parameters of links and joints. The following Denavit-Hartenberg parameters are used for the links and articulations of the robot manipulator:
The
The parameters
The following algorithm is used to determine the Denavit-Hartenberg parameters:
- Rotation of the
st system around the axis clockwise (visually viewed from the point ) at an angle until the axis becomes parallel and unidirectional to the axis . - Shift of the rotated
st system along the axis by the dimension to the alignment of the axis with the axis. - The shift of system
st along the axis by the value until the starting points of the coordinates of systems and do not coincide. - Rotation of the
st system around the axis clockwise (when viewed from the point ) by an angle until the нaxis is aligned with the axis.
As a result of the above algorithm, the parameters of the links and joints of the DMRA robot are as follows (Table 1).
Construction of uniform transformation matrices. Each homogeneous matrix of transformations (transfer matrix) matches the coordinates of the
|
(1) |
|
(2) |
Taking into account Table 1 and formulas (1) and (2), we have the following transfer matrices for each articulation
|
(3) |
|
(4) |
|
(5) |
|
(6) |
|
(7) |
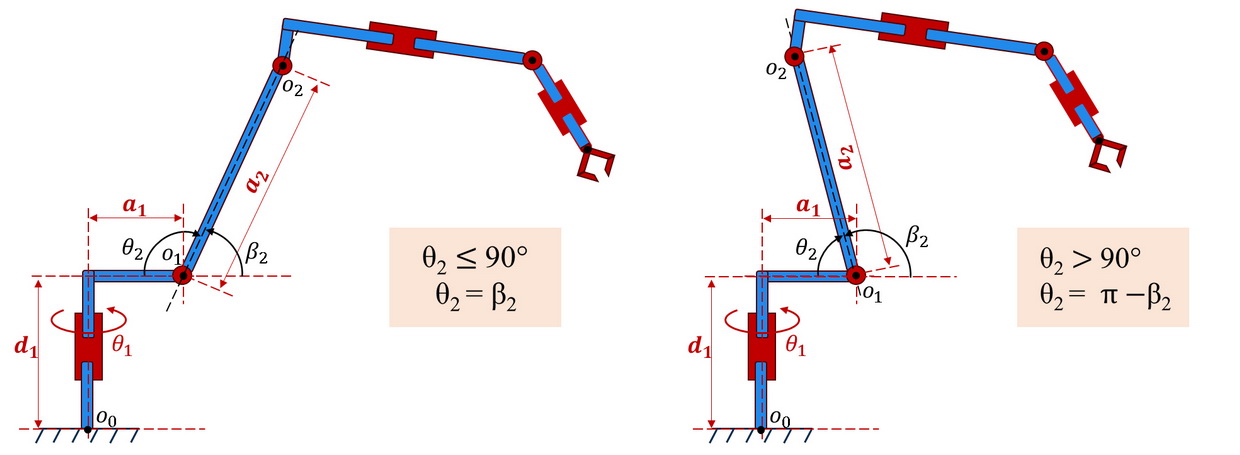
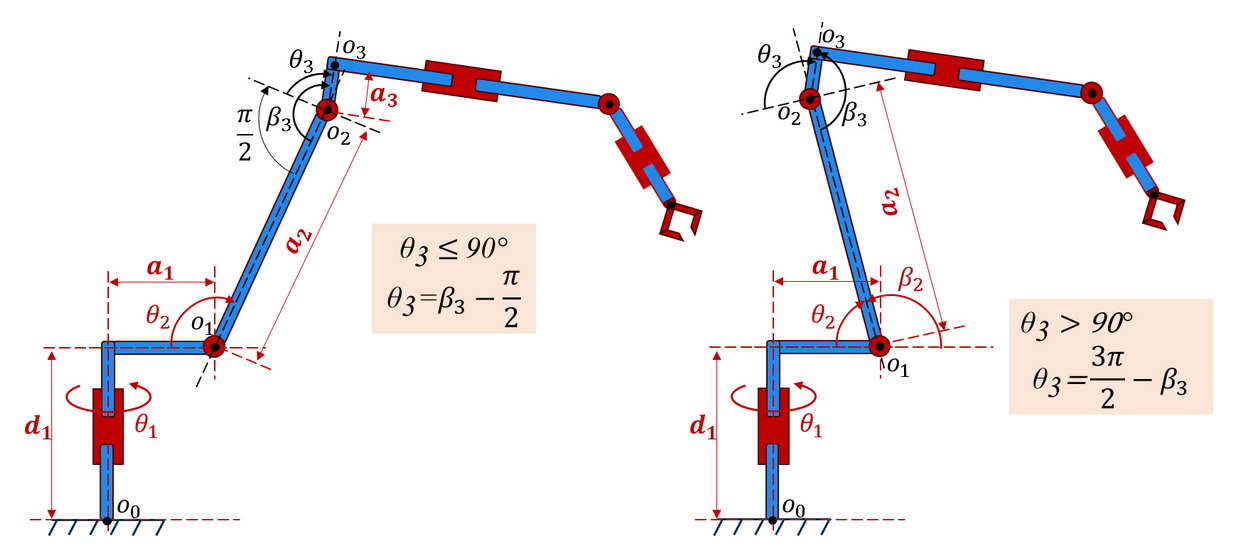
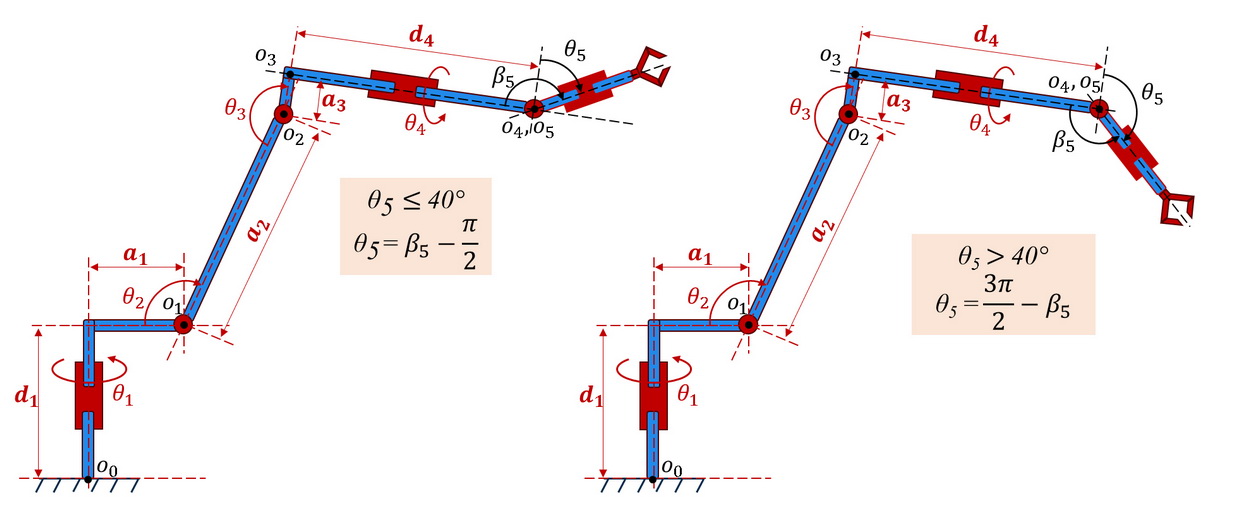
Using formulas (3)...(7), it is possible to obtain the coordinates of the
|
(8) |
Since the